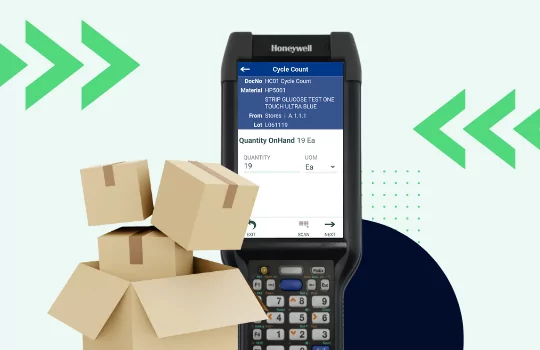
Warehouse Manager’s Playbook for Automation Success
More than half of warehouse leaders say seamless compatibility with existing equipment is a non-negotiable. If you’re staring down labor shortages, rising error rates, or another fiscal year of overtime spikes, it might be time to revisit your automation strategy or build one from the ground up.
This Warehouse Manager’s Playbook offers an actionable roadmap to help you evaluate, pilot, deploy, and optimize warehouse automation with minimal disruption and maximum ROI. Whether you’re managing a single facility or a multi-site network, this step-by-step guide is built for hands-on leaders ready to modernize operations.
Step 1: Assess Your Readiness
Before investing in automation, it’s critical to benchmark your current warehouse environment. Use this six-factor framework to assess readiness across the following criteria:
- Technology: Do your WMS/WES systems support API or middleware integrations?
- Volume: Are order volumes stable, seasonal, or scaling quickly?
- Labor: How are labor shortages and turnover impacting workflows?
- Accuracy: Are picking and packing errors causing costly rework or returns?
- Safety: Are there ergonomic risks, repetitive motion injuries, or collision-prone zones?
- ROI Potential: Can automation measurably reduce costs or improve service levels?
Based on this analysis, pinpoint 3 pilot areas that will provide the most value with the least disruption. These areas might include manual picking zones, repetitive packing stations, or staging lanes with high congestion.
Step 2: Select the Right Automation Solution
No two automation paths are the same. Some warehouses benefit from modest automation, such as pick-to-light systems or mobile barcode scanning apps, while others are ready for advanced solutions like autonomous mobile robots (AMRs) or automated storage and retrieval systems (AS/RS).
Use these criteria to evaluate your options:
Criteria | Why It Matters |
Durability | Systems should withstand warehouse wear and tear over 5+ years. |
Integrability | Seamless integration with existing WMS/WES reduces complexity. |
Modularity | A modular design enables incremental rollouts zone by zone. |
Support | Ongoing vendor support and maintenance should be easy and accessible. |
To mitigate risk, start with a small pilot zone of just 10 to 20 square feet and validate both technical performance and human adoption before scaling.
Step 3: Follow a Four-Phase Deployment Framework
Once you’ve selected your automation solution, execute with discipline using a four-phase deployment model:
1. Plan
- Develop a RACI matrix to identify responsible stakeholders.
- Coordinate site prep, including power, Wi-Fi, and safety clearance zones.
- Schedule go/no-go timelines and set clear KPIs for the pilot.
2. Pilot
- Select and train a small group of floor champions.
- Run the system for at least two weeks, gathering performance data and worker feedback.
- Address real-world issues like software bugs or sensor misreads in real time.
3. Roll-Out
- Gradually expand the system to an entire zone or shift.
- Deploy standard operating procedures (SOPs) for new workflows.
- Monitor performance continuously and compare against pre-pilot benchmarks.
4. Optimize
- Set up real-time dashboards to monitor KPIs (more on that below).
- Conduct quarterly performance reviews to fine-tune system configurations.
- Capture and act on worker suggestions for continuous improvement.
Step 4: Manage Change on the Floor
Even the best automation system can fail if your people don’t buy in. Change management is essential, especially in warehouses where the workforce may be unfamiliar or skeptical about robotics.
Key strategies to build trust and reduce resistance:
- Appoint Floor Champions: These are respected peers who can lead by example, answer questions, and de-escalate concerns.
- Hands-On Workshops: Let workers interact with the technology before go-live. This builds confidence and comfort.
- Run Safety Drills: Show how the system detects and avoids humans, and establish clear safety zones and emergency protocols.
- Real-Time Feedback Loops: Encourage continuous feedback via QR codes, suggestion boards, or mobile apps, and make workers feel heard.
This combination turns anxiety into ownership and helps create a more resilient, tech-savvy workforce.
Step 5: Track KPIs and Drive Continuous Improvement
Without real-time performance visibility, automation can become just another siloed system. That’s why tracking key metrics is essential, especially in the early stages.Prioritize the following KPIs:
KPI | Target |
System Uptime | ≥ 97% |
Pick Accuracy | ≥ 99.5% |
Throughput (Pick Rates) | Baseline vs. post-deployment improvements |
Labor Savings | Percent reduction in manual tasks per shift |
Solutions like RFgen dashboards enable real-time alerting, root-cause tagging, and easy-to-share reports. These dashboards help identify issues early, such as throughput dips or scanner errors, and provide a central system of record to optimize performance.
Step 6: Scale and Future-Proof
Once automation proves its value in one zone, the path to scaling becomes clearer. However, avoid the trap of scaling before systems and teams are fully stabilized.
Here’s how to prepare for long-term success:
- Introduce Robotics-as-a-Service (RaaS) for seasonal or temporary fulfillment peaks without the capex burden.
- Use open APIs like those in RFgen to integrate new robots or automation modules from different vendors.
- Stay ahead of trends by preparing for next-gen technologies like AI-enabled vision systems or collaborative robots (cobots).
According to SCMR’s 2025 Warehouse Automation Survey, 78% of operations leaders plan to expand their automation investments by 2026. The time to build a scalable and future-ready system is now.
The Bottom Line: Smart Execution Wins
Warehouse automation doesn’t have to be disruptive or high risk. By starting with a readiness assessment, choosing the right solution, managing change effectively, and tracking results obsessively, you can turn automation into a competitive advantage.
More importantly, you can create a warehouse environment that is:
- Safer for your people
- More responsive to market demand
- >Better prepared for future growth
Want more insights on where warehouse automation is headed next? Read MIT’s outlook on the warehouse of the future or explore how RFgen helps you simplify integration and drive ROI with mobile and robotic solutions.